VRF System Cost
We know that VRF system cost varies based on many factors which must be considered when budgeting or bidding on a commercial HVAC project. Of course, it’s not the best option to provide a GMP (Guaranteed Maximum Price) based on a parameter such as cost per square foot or cost per ton.
Using cost parameters is beneficial when called upon to provide a budget or to double check a current bid for alignment with your historical project cost data. Whether you are an Engineer providing a budget to the Architect or owner, or an HVAC Contractor, the following consideration of cost apply.
Project Historical Cost Data
Maintaining historical cost data is in your best interest if you plan on being in the HVAC industry for a career. Having cost data is useful whether you’re an engineer or an HVAC contractor.
Knowing how much a VRF System cost or any HVAC system is important to your business. Having a spreadsheet that records all the pertinent cost data of completed projects or bids will allow you to use that cost data to compare against a proposed buildings square footage or installed tons.

Historical data is great for saving time and money when an owner or a General contractor request a quick budget. Having a cost database of previous projects is a smart approach to being responsive to your customers’ needs for quick cost values. Or are you one of the fortunate ones that never get a request for a budget that is due with very little notice or time to complete?
VRF System Cost per Square Foot
When comparing the VRF System cost or other HVAC Systems from one building to another, it’s important that the buildings share the same characteristics or you make adjustments for the differences.
Just like a real estate appraiser makes adjustments for differences between homes, such as differing amenities and finishes, the HVAC budget between buildings needs to be adjusted for differences.
There are parameters that you want to save in your cost database that are related to building characteristics. For example, building use (Office, School, Hotel, etc.), the quantity of floors, type of structure (wood, concrete), height of building, new construction or retrofit, floor to floor height, etc.
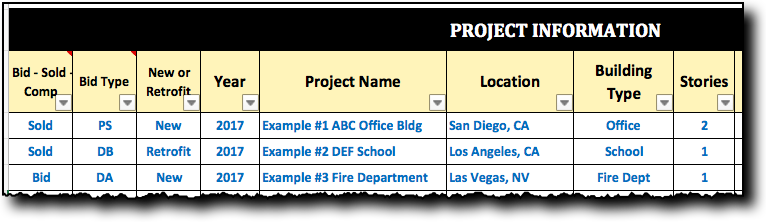
In addition to building characteristics there are job conditions that have an impact on project cost such as: Project access, stacking of trades, security clearances, working height, dust or sound control measures, project meeting & safety requirements. Each project is unique at least in the commercial HVAC sector.
VRF System Cost per Ton
Similar to the VRF System Cost per Square Foot, using tonnage as a parameter for comparison has several things to be considered in addition to the ones discussed above. In addition to the characteristics of the building, you’ll need to evaluate the differences between VRF Systems types and components.
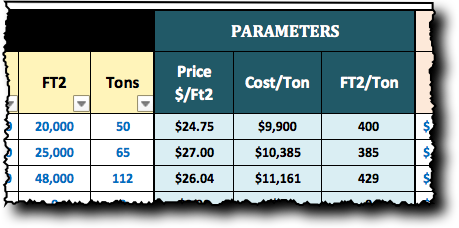
Are you comparing a VRF Heat Pump system or a VRF Heat Recovery System? Is this a three-pipe system or a two-pipe VRF system? Are there single port branch selector boxes or all multi-port boxes? How many fan coils? How many Main Controllers? If you are installing another type of HVAC system, then the pertinent data for that system type needs to be recorded in your historical database.
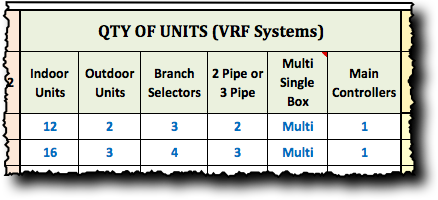
VRF System Cost per HVAC Contractor
There are many factors that can impact the cost of an HVAC system between contractors. Each HVAC contractor has a different business model and cost structure that impacts their HVAC installed cost.
If you are an engineer doing a budget for an owner or Architect it is imperative that you understand who the targeted HVAC contractors will be for the project.
- Will there be Union or Non-Union HVAC contractors bidding on the project?
- Is the project for a municipality where prevailing wages are required?
- Is the project located in a Union dominated city like San Francisco or New York?
Impact of Labor Rates on VRF System Cost
HVAC systems and VRF System Cost are impacted by the HVAC contractors cost for skilled labor. If the HVAC contractor is a Union affiliated company then these labor rates are dictated by the union located near the project site.
If the project is located in the city of San Francisco or New York there is a good chance that you will be dealing with a Union contractor. Was the project executed on overtime or straight time or a combination? Unions usually have scheduled labor rate increases that occur semi-annually or annually.
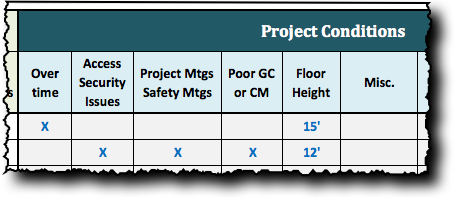
Impact of Material Cost on VRF System Cost
Another factor to consider is the current state of the economy and the cost of commodities. Is the cost of copper going up or down? VRF projects are heavy users of ACR Copper. When will the project be built, this year or next year?
Material escalation can be accounted for if you know when the project will be built. You can review the PPI (Producers Price Index for Copper) year over year as a percentage and add that value to your material cost as state as such in your proposal. What does your material or equipment cost per square feet for the various projects?
Impact of Time on VRF System Cost
Each year the cost of labor and material mostly goes up due to inflation. Is the HVAC project you are considering being built this year or next year? What is the duration of the project? It’s important to know when the project is being built and the duration.
If you are an engineer putting together a budget for the Architect or owner it’s imperative that you qualify your budget based on time, as time has a value. In large projects that will be built over several years or that won’t start for another year or even latter as owners are often looking for the right economic and strategic time to expend cost for a project.
It’s important to qualify your proposal, whether an Engineer or HVAC contractor, bringing awareness to the cost impact due to time. This is often accomplished by HVAC contractors by putting an expiration date on the proposal, but that date often gets forgotten during negotiations with the General contractor or owner, and the HVAC contractors desire to close a sale.
In the interest of all parties it’s a good idea to bring the cost factor of time into the proposal by highlighting the cost impact due to escalation of labor and material cost for projects delayed until a later time period.
Due to the unpredictability of the material and labor markets this budget is subject to increase due to the economic climate at the time of contract, which may differ substantially from the current environment.
Impact of Delivery Method on VRF System Cost
Is the project based on a set of plans and specifications designed by an engineer or is this a design/build project? The delivery method can have an impact on the project timeline, cost and quality of work.
Tracking your projects based on the type of delivery method will let you know which projects produce the best results based on profit margins.
My historical data shows that greater project margins are made with design/build projects, but you may find a different result. You won’t know unless you track your projects. This goes for any HVAC project, irrespective of the type of system.
Engineering Parameter
Another useful piece of information is how many Ft2/Ton was engineered for each project. When given an architectural background or just the total square feet of a proposed project you can use this data to come up with the total tons required and then use your other cost parameters to arrive at the total cost.
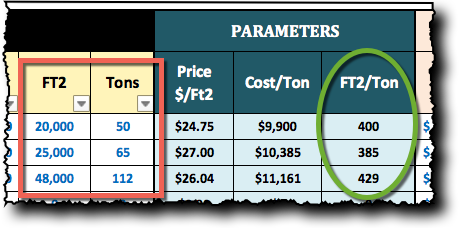
VRF System Cost Summary
No matter which parameter you use the VRF System cost per square foot or cost per ton, you will need to use historical data that relates to your current project and make an educated adjustment as needed. You will also need to consider escalation for any duration beyond the immediate construction of the project.
As you can see there are many variables to pricing a VRF or HVAC project, and anyone that tells you it cost a certain amount per square foot or ton, you should be specious of, as no one value can possibly cover all project variables of the installed cost of an HVAC system.
Each project has characteristics that change the installed cost and having a database from which to compare is a valuable asset for any Engineer or HVAC contractor. Using a Project Cost Database that contains all the pertinent parameters of a project including engineering and cost data will save you time and money while giving you the best opportunity to provide the most accurate budget for your customer.
You can spend hundreds of hours building a project cost database or you can get one the VRFWizard Project Cost Database. This database can be used for all HVAC system types, not just for VRF System Cost. Get the VRF Wizard Project Cost Database for just $99 See the NEW Updated Version of the VRF Cost Tracking Spreadsheet here.